Acrylonitrile styrene acrylate, also known as ASA, is an engineering thermoplastic with a similar molecular structure to the very popular and commonly used acrylonitrile butadiene styrene, a.k.a. ABS. ASA is known for its high impact and good chemical resistance. It can handle high temperatures (softening at 105 °C) and has great dimensional stability.
Compared to ABS, ASA is UV-stable and maintains its appearance and resistance even after long exposure to sunlight and water. It’s in many common products, including auto parts (bumper covers and side mirror housings), gutter and drain pipes, and outdoor furniture.
In the All3DP office, we’ve had great experiences making functional ASA parts on popular desktop printers like the Original Prusa MK4 and the Creality K1. The built-in enclosure of the K1 was particularly useful to avoid some of the common pitfalls of ASA printing.
In the following, we’ll take a look at some of the advantages and disadvantages of ASA before moving on to what’s necessary to print with the material, considering both hardware and software aspects.
If you already have a design in mind and you simply need to print it in ASA, consider using a 3D printing service. With Craftcloud by All3DP, you’ll instantly find the best price and provider based on your models and location. And the best part is, there are no added fees!
Pros & Cons

While PLA is perhaps the most-consumed material for FDM 3D printing, ABS is frequently used for high-resistance applications such as functional or outdoor parts. Unfortunately, it has a few printability drawbacks, which are also seen in ASA due to their shared heritage. Most of these drawbacks are less present in ASA, though, making this material a bit easier to print.
Pros
- UV stable (great for outdoors)
- Tough and durable
- High impact and temperature resistance
- Great resistance to chemicals and water
- Good overall finish
- Soluble in acetone (for gluing and smoothing)
- Compatible with soluble support (HIPS)
Cons
- Requires higher extruder and bed temperatures
- Prone to warping, cracking, and shrinking during 3D printing
- Potentially dangerous fumes
- Expensive
Hardware Requirements
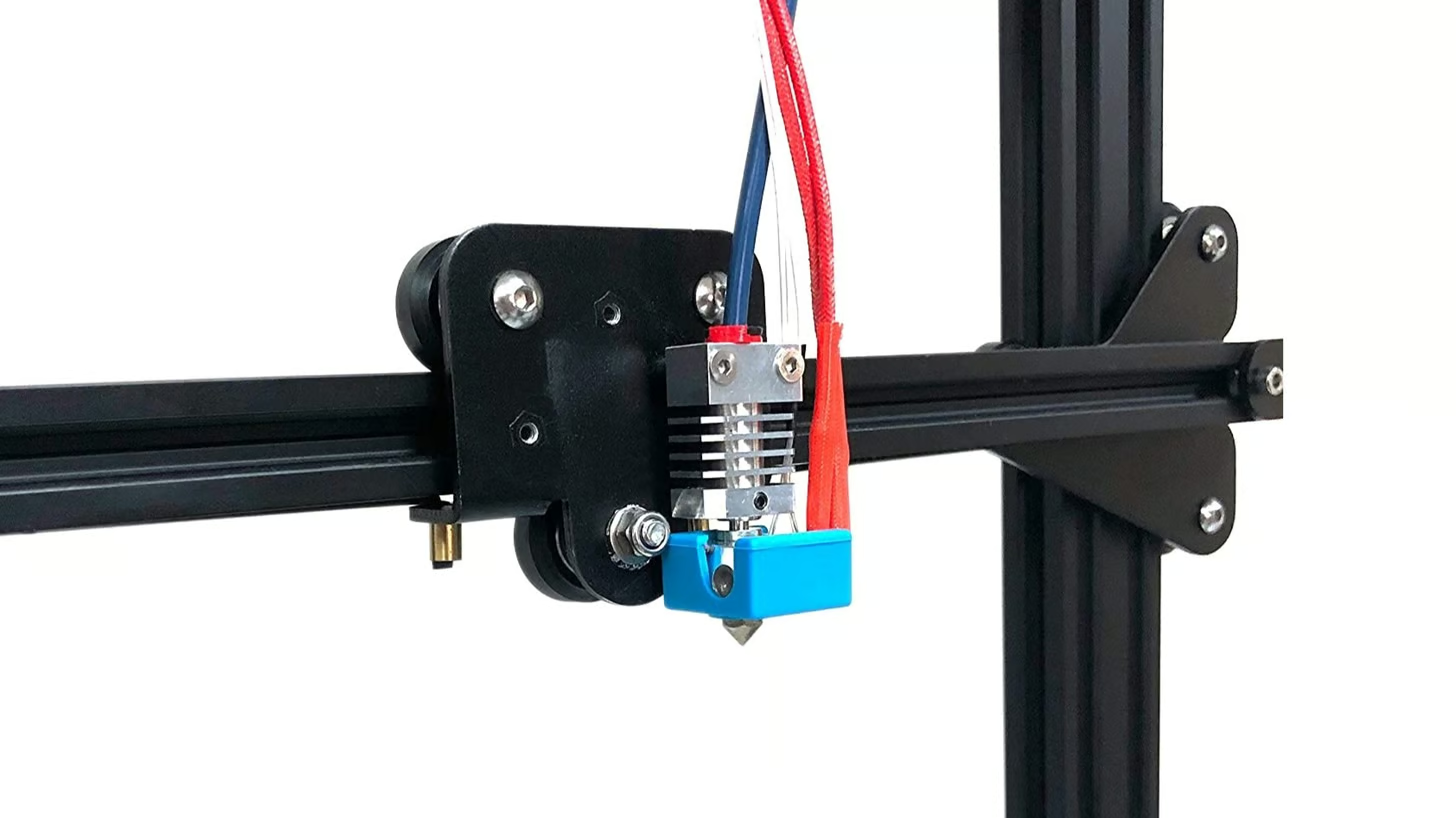
Before even considering using ASA, make sure your 3D printer meets the following hardware requirements. This will definitely save you a headache in the future.
- Heated bed: This is mandatory. ASA is prone to shrinking and cracking due to the temperature difference between the nozzle and the surrounding air. The thermal deformation caused by this disparity creates internal tensions that potentially lead to problems during the printing process.
- Build surface: Proper bed adhesion is essential for ASA, and for this, there are dozens of solutions. Many use Kapton tape, coating solutions such as ABS glue, or standard hairspray. As with any other material that depends on good bed adhesion, make sure your bed is always properly leveled.
- Enclosed printer: This is highly recommended, especially when printing large parts. Though it’s possible to get away with printing smaller parts without an enclosure, larger models will produce a lot of residual stress that can eventually cause cracking and delamination. An enclosure also protects the 3D printer from drafts that will most certainly cause parts to warp.
- High-temperature hot end: No special hot end is required as long as it can print at temperatures as high as 260 °C. PTFE-lined hot ends might not be suitable for longer periods of ASA printing since PTFE starts degrading at 250 °C. While some ASA filament brands can be printed with temperatures lower than 250 °C, an all-metal hot end is surely the safer choice.
- Filament storage: ASA is hygroscopic, meaning it absorbs moisture from the air. This moisture can cause extrusion inconsistencies and surface defects, among other issues. Therefore, it’s important to store ASA in a dry box.
Print Settings
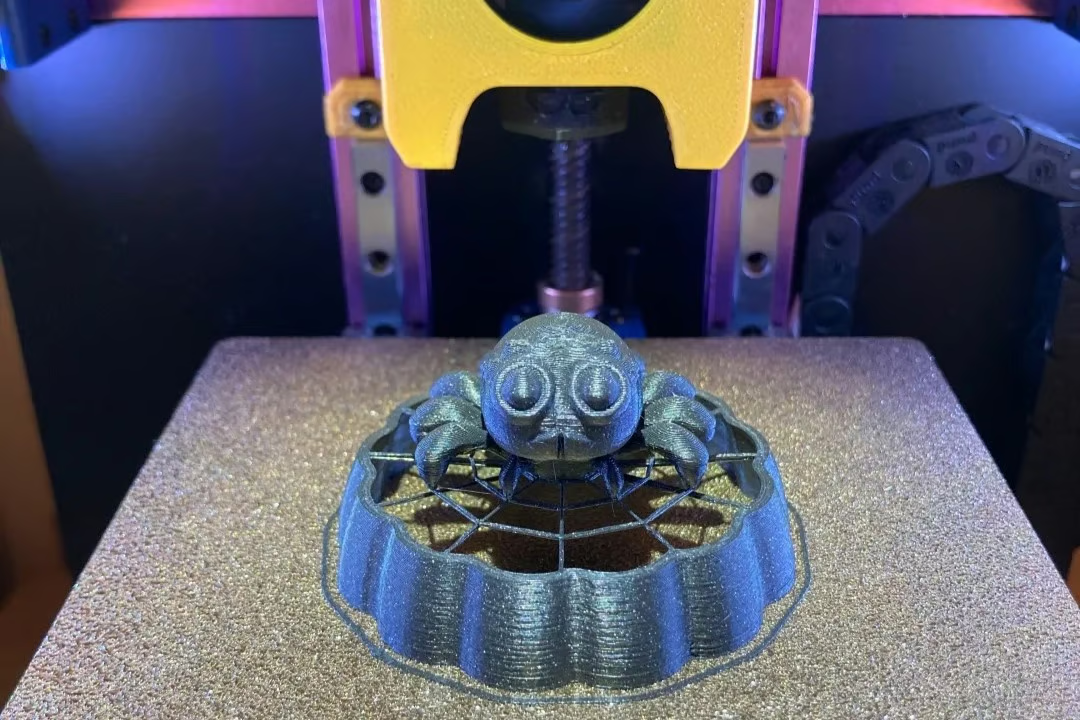
If all the hardware requirements are met, it’s time to fine-tune the print settings:
- Bed temperature: For ASA, it’s recommended to have the build plate temperature set between 90 and 110 °C, depending on the filament brand. Be sure to let it sufficiently preheat before starting a print (this will also heat the print chamber).
- Nozzle temperature: This material prints at a relatively high temperature, usually falling within the 240 to 260 °C range. Generally speaking, go higher when you notice poor layer adhesion and go lower if you notice sagging bridges, stringing, or oozing. It’s suggested to decrease the temperature for the first layer by 5-10 °C.
- Print speed: Generally, the best speed for printing ASA will be between 40 and 50 mm/s. To help improve bed adhesion, you can try printing the first layer at 25 mm/s. Reduce your print speed if you’re noticing layer adhesion issues.
- Cooling: No cooling is required for printing with ASA. In fact, it’s generally recommended to leave it off. However, very low speeds (5 to 10%) might improve overhangs and overall print quality. We suggest first focusing on having good layer adhesion, and once that’s achieved, try using the cooling fan to avoid overheating issues.
Other settings, such as layer height and infill, will depend on your specific printer, filament, and project. We suggest using the default settings for your specific filament brand and tweaking them to suit your needs.
For example, if you’re going for functional parts that need high strength, you may want to use upwards of 50% infill, however, using much higher infill content can make the part more prone to warping. The infill pattern can also help increase your print’s strength. You can get away with 20% infill for aesthetic prints, but don’t go lower as the part will be more susceptible to cracking.
Challenges
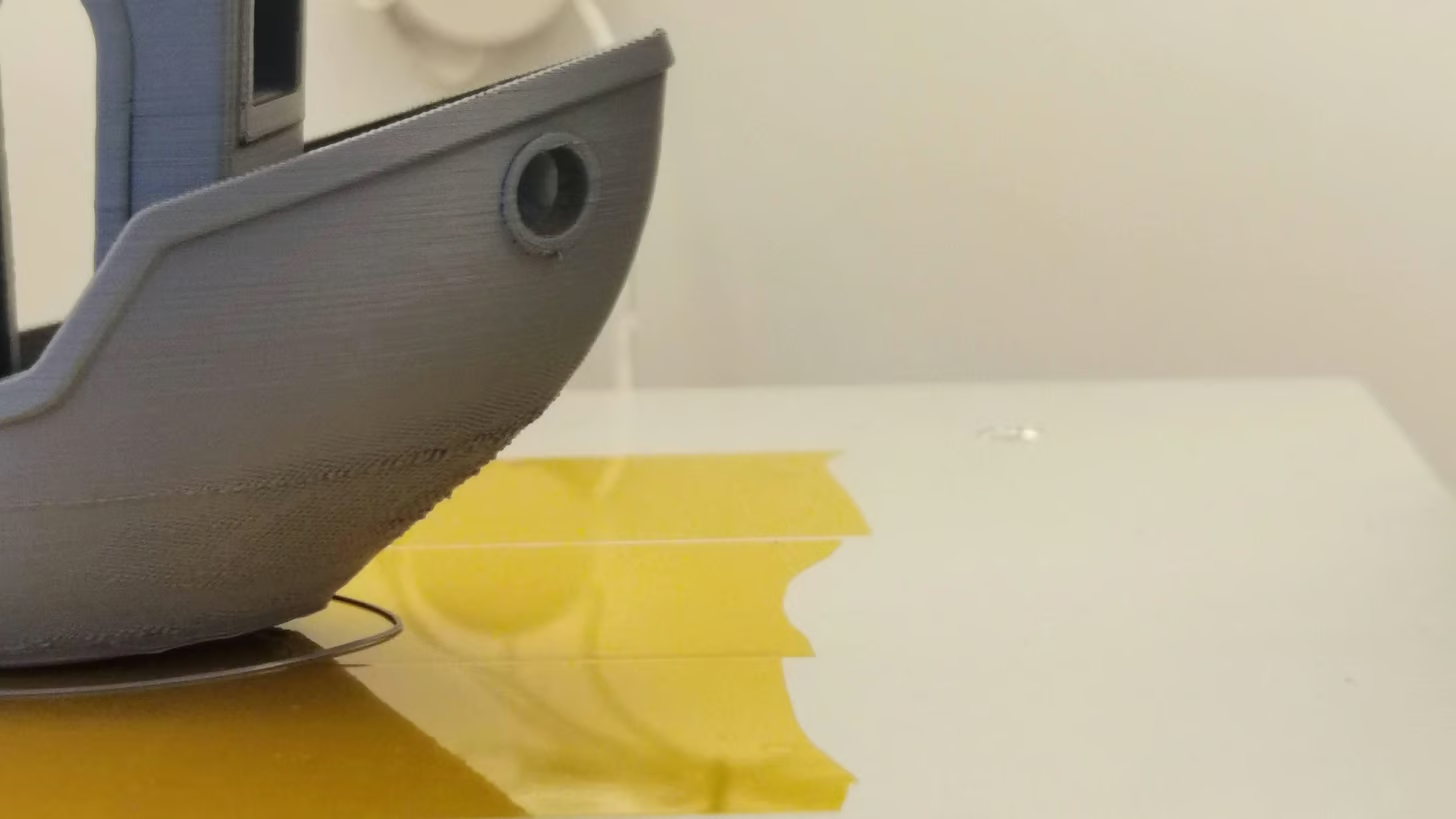
Printing with ASA can have its difficulties because it can be terribly sensitive to temperature changes. The good news is that ASA is still easier to print with than ABS.
As mentioned earlier, perhaps the most pressing issues when working with ASA are the warping effects and the potentially dangerous fumes that can be released.
Warping
Warping happens when the part fails to cool evenly. There’s plenty of information on avoiding warping during FDM printing, which is mostly with ABS. And since these two materials are so similar, it’s a good idea to follow the same recommendations: avoid wind drafts, ensure good first-layer adhesion, keep your printer calibrated, and use brims or rafts.
Fumes
As for the fumes, most printing materials release some kind of harmful substance during extrusion. Perhaps the most famous one is ABS, known to emit both dangerous gaseous molecules and nanoparticles. Although less troublesome than ABS, printing with ASA can be a very smelly process – mostly due to the presence of styrene. However, if you’re noticing strong smells, you may want to decrease the printing temperature slightly.
Proper ventilation is strongly recommended along with the use of masks, if appropriate.