The vast majority of fused-deposition modeling (FDM) 3D printers have either direct or Bowden extruders. And while the basic principle is the same – the use of an extruder to push filament through a heated nozzle – the difference lays in where that extruder sits.
Direct extruders are mounted on the printhead and pushes the filament directly into the hot end. Meanwhile, Bowden extruders usually have the extruder mounted on the frame of the printer. As such, the filament travels through a PTFE tube to reach the printhead.
Thanks to advances in hardware, the availability of lighter weight direct extruders has increased, making them more prevalent. Creality as well as other manufacturers of budget 3D printers have made the shift. Both Ender 3 V3 models feature direct extruders. We even see small cantilever printer designs such as Bambu Lab’s A1 Mini with lightweight direct extruders mounted on their printheads.
As many in the 3D printing community have said, there’s still a place for Bowden extruders despite the ascendancy and prevalence of direct extruders. In this article, we’ll dive in the the pros and cons of both options.
Direct Extruders
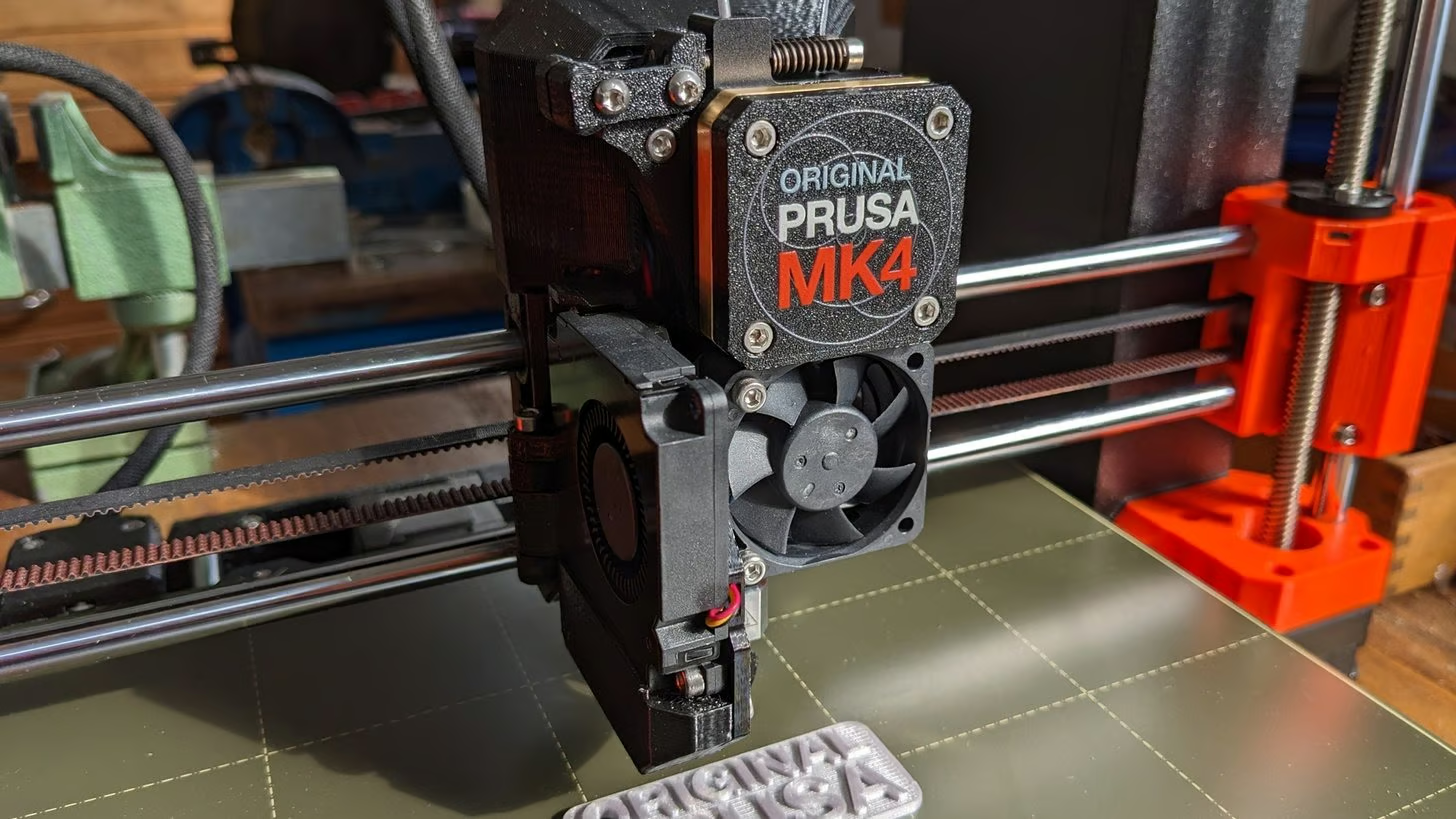
Direct extruders push filament directly into the nozzle. This method is helpful for many reasons, but it also has some downsides. Let’s take a look.
PROS
- Reliable extrusion: Since a direct extruder is mounted to the printhead, the motor can easily push filament through the nozzle, allowing for more precision and control over filament delivery.
- Better retraction: Because the extruder is close to the nozzle, it can more easily retract filament.
- Less-powerful motor: Due to the short distance between the extruder and the nozzle, less torque from the motor is required to push the filament.
- Wider range of filaments: Although less relevant now compared to the early RepRap days, a direct extruder is generally considered to be more compatible with a wider range of filaments. This is especially the case with flexible and abrasive materials.
CONS
- Vibrations: With the extruder mounted to the printhead, weight is obviously added. This extra weight adds speed constraints, causing more wobble and possibly a loss of accuracy in X and Y movements.
- Cumbersome maintenance: In some setups, the extruder being mounted to the printhead can make accessing certain parts for maintenance more difficult.
3D printers that have direct extrusion setups include Bambu Lab’s A1 and A1 Mini, Prusa’s i3 MK4, and Creality’s Ender 3 V3 SE and KE printers.
Bowden Extruders
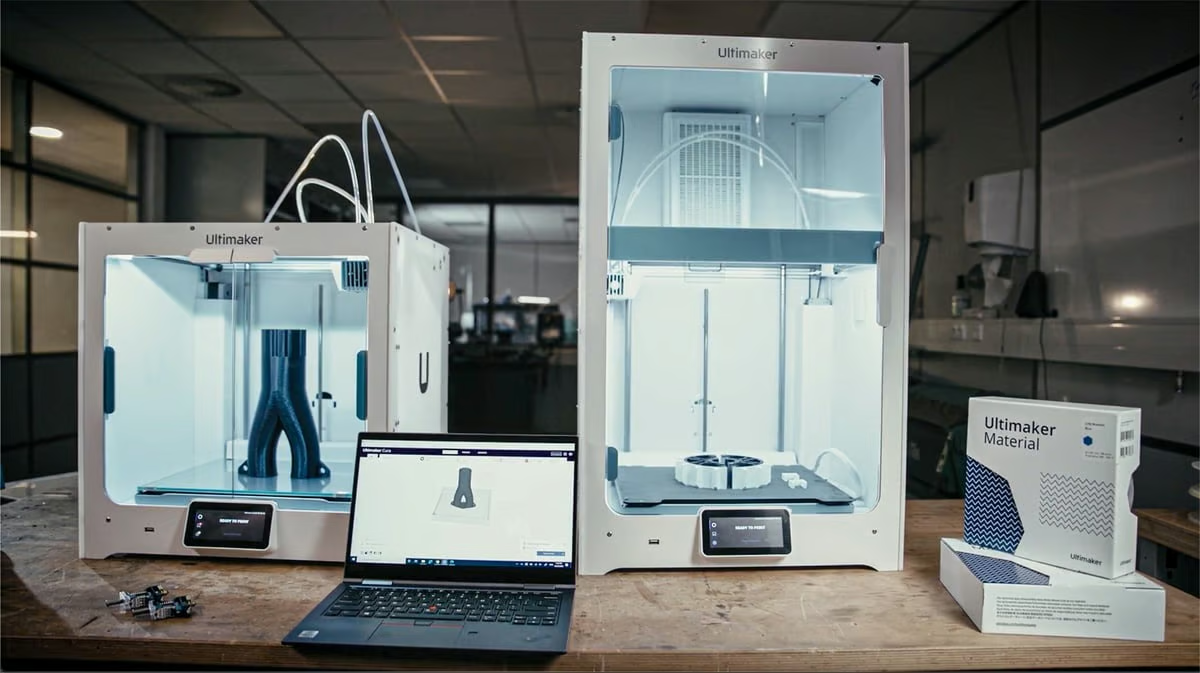
Unlike in a direct extrusion setup, in a Bowden system, the extruder is mounted on the printer’s frame. It pushes and pulls filament through a long PTFE tube (called a Bowden tube) and into the hot end. Naturally, this system also has pros and cons.
PROS
- Cleaner movements: As a Bowden extruder is mounted on the printer’s frame rather than on the printhead, much less weight is on the carriage. Less weight means faster, quieter, and higher quality prints.
- Larger build volume: Though not always the case (depending on a printer’s construction), the Bowden extruder’s placement on the printer’s frame may allow for a smaller printhead carriage, which may in turn allow for increased build volume.
CONS
- More powerful motor: Because the extruder must push and pull filament through a long tube, a certain amount of friction exists between the two. This friction calls for more torque to adequately control the filament.
- Slower response time: Given the feed distance from the extruder to the printhead, there’s a noticeable delay in response time, which can be acerbated if the filament bends inside the PTFE tube and causes friction. A longer retraction distance and faster retraction speed are typically required to avoid extrusion issues.
- Material complications: Some flexible and abrasive filaments can easily bind or wear in Bowden tubes, especially in older models of printers.
To name a couple, UltiMaker’s S7 and Prusa’s Mini+ have Bowden extruders. Additionally, Voron printer models have a history of using Bowden extruders, and two versions – the Mobius (M4) and Nightwatch – are currently available for builds.
Final Thoughts
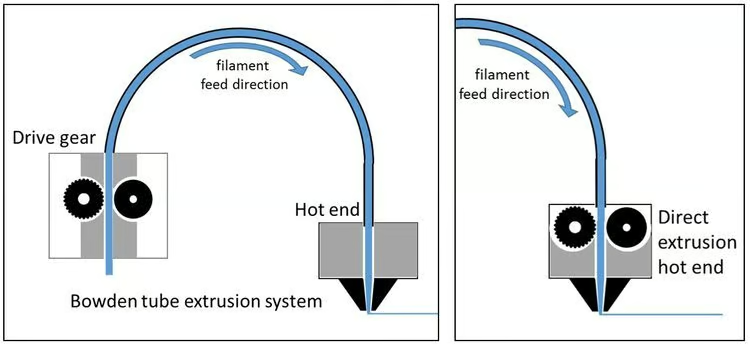
So, which system is better? It depends. Before you decide which extrusion option to use for your printer, you should consider some important factors.
The first is frame and motion system stability. Many delta printers, for example, can’t easily support the weight and vibrations that come with a direct extruder. If, however, your Cartesian or CoreXY printer has a sturdy structure, printing with a direct extruder should be no problem.
Speed is also a deciding factor. If your priority is fast, precise printing with standard materials, a Bowden extruder will be more satisfactory.
Lastly, you should consider the materials you would like to print with. If you’re interested in flexible or abrasive filaments, a direct extruder is likely the one for you.
You don’t need to fret if you’ve already got your 3D printer and want to change from a Bowden to a direct extrusion setup; check our guides for the Ender 3 (V2/Pro) and 5.